
论工业4.0时代生产设备规模化升级中减振管理的重要性
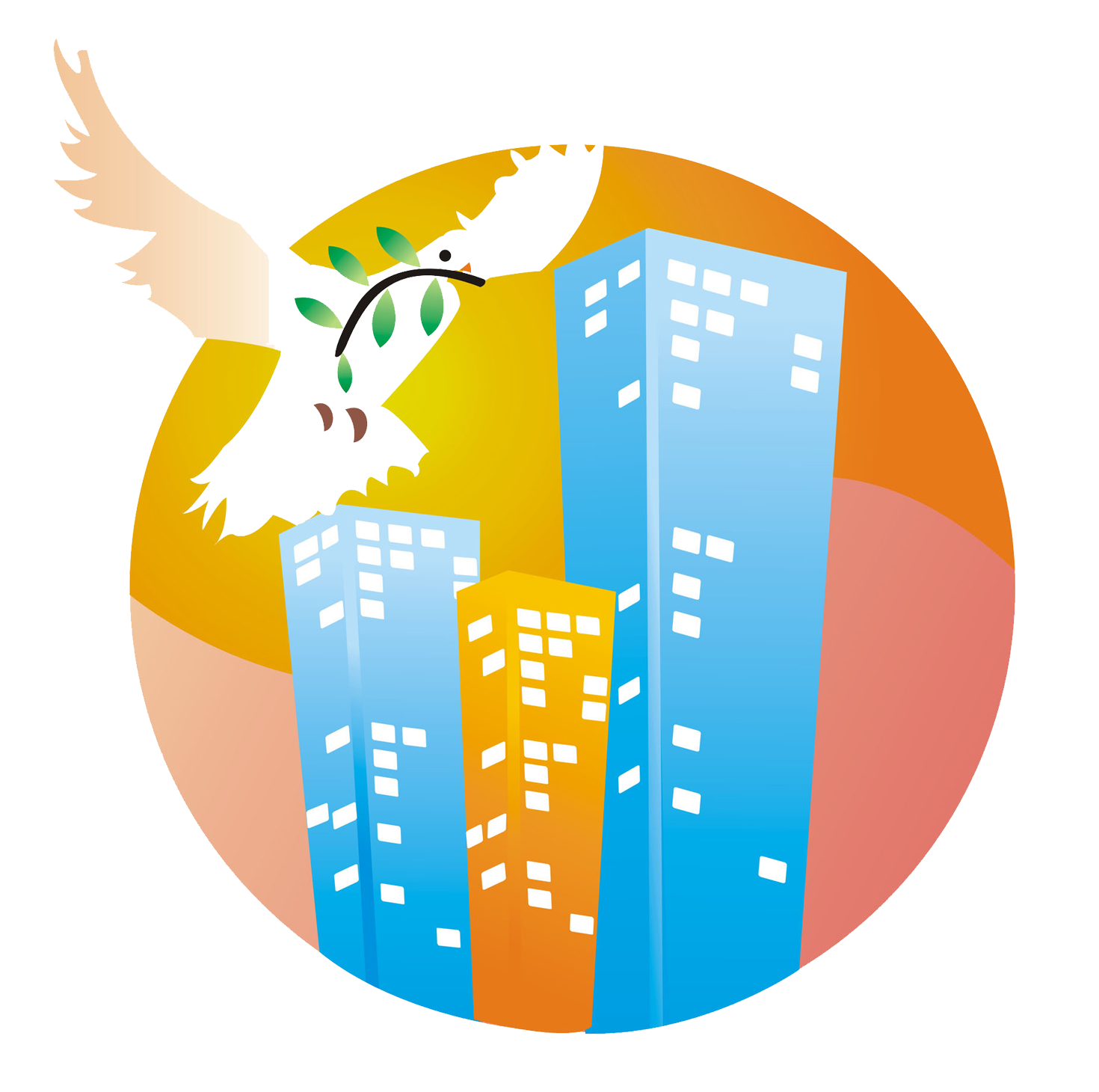
在高质量发展前提下,工业4.0时代生产设备的减振管理已成为提升设备性能、保障产品质量、降低生产成本、促进绿色制造的关键环节。
减振管理中的减振材料是至关重要,传统减振材料在材料性能、环境适应性、吸能效率等方面存在局限性,同时设备升级带来的新挑战也加剧了这些局限性。因此,开发新型高性能减震材料成为满足现代工业需求的必然选择。
传统减振材料在工业设备规模化升级中失效的原因,可归纳为以下四大核心矛盾,结合实例与数据为您详细解析:
一、材料本征性能与复杂工况的失配
高频振动过滤失效
传统材料(如橡胶、乳胶、泡沫、EPP)依赖压缩形变进行吸能,对高频振动(>1000Hz)和低幅值冲击(<0.1g)的过滤效率不足,并且容易开裂。例如,精密数控机床在微振动环境下,传统减震垫导致加工精度误差从0.01mm扩大至0.05mm。极端环境耐受性差
橡胶类材料在-40℃低温下硬度增加30%-50%,导致密封失效、老化;高温下(>80℃)则加速老化,阻尼系数下降40%。某化工厂传统减震器因温度变化频繁,3年内更换率达82%。
二、设备升级带来的多维挑战
振动模态复杂化
现代设备(如工业机器人)振动频率从单一频段扩展至多频段(如5-500Hz混合振动),传统材料无法同步衰减多频振动能量。轻量化与空间约束
传统减振器减震垫厚度体积是新型材料的2-3倍,无法满足半导体设备的紧凑设计需求。例如,传统弹簧减震器占用光刻机内部空间达15%,而新型材料制成的减震器可压缩至5%以下。
三、失效机制与全生命周期成本
分子链疲劳断裂
橡胶材料在反复受力下,分子链断裂周期仅3-5年,导致硬度增加、阻尼性能下降。某风电场齿轮箱传统减震垫5年更换成本占运维预算的2%。环保与可持续性危机
传统EVA泡沫含卤素阻燃剂,废弃后难以降解,处理成本高达材料价值的60%。欧盟已立法限制此类材料在精密设备中的应用。
四、产业升级的技术代际差
智能化需求断层
传统材料无法集成传感器或自适应调节功能,而现代设备(如自动驾驶汽车)需减震材料具备实时刚度调节能力。性能天花板效应
传统材料吸能效率上限为60%-70%,而新型减振超材料(如ACF人工软骨材料)吸能效率高达97.1%,寿命长,轻量化,防静电,抗腐蚀、良好的阻燃性,能够适应复杂工况下的减振需求。
结论:传统减振材料失效的本质是工业4.0时代设备对减振系统提出了"多频适配、智能调控、极端环境耐受"的三重需求,而传统材料仅能满足单一维度的基本功能。产业升级需采用仿生设计、纳米增强等新技术,开发如ACF超材料这类具备多相协同机制的新型减震方案。