
工业生产中传统减震缓冲材料的局限性
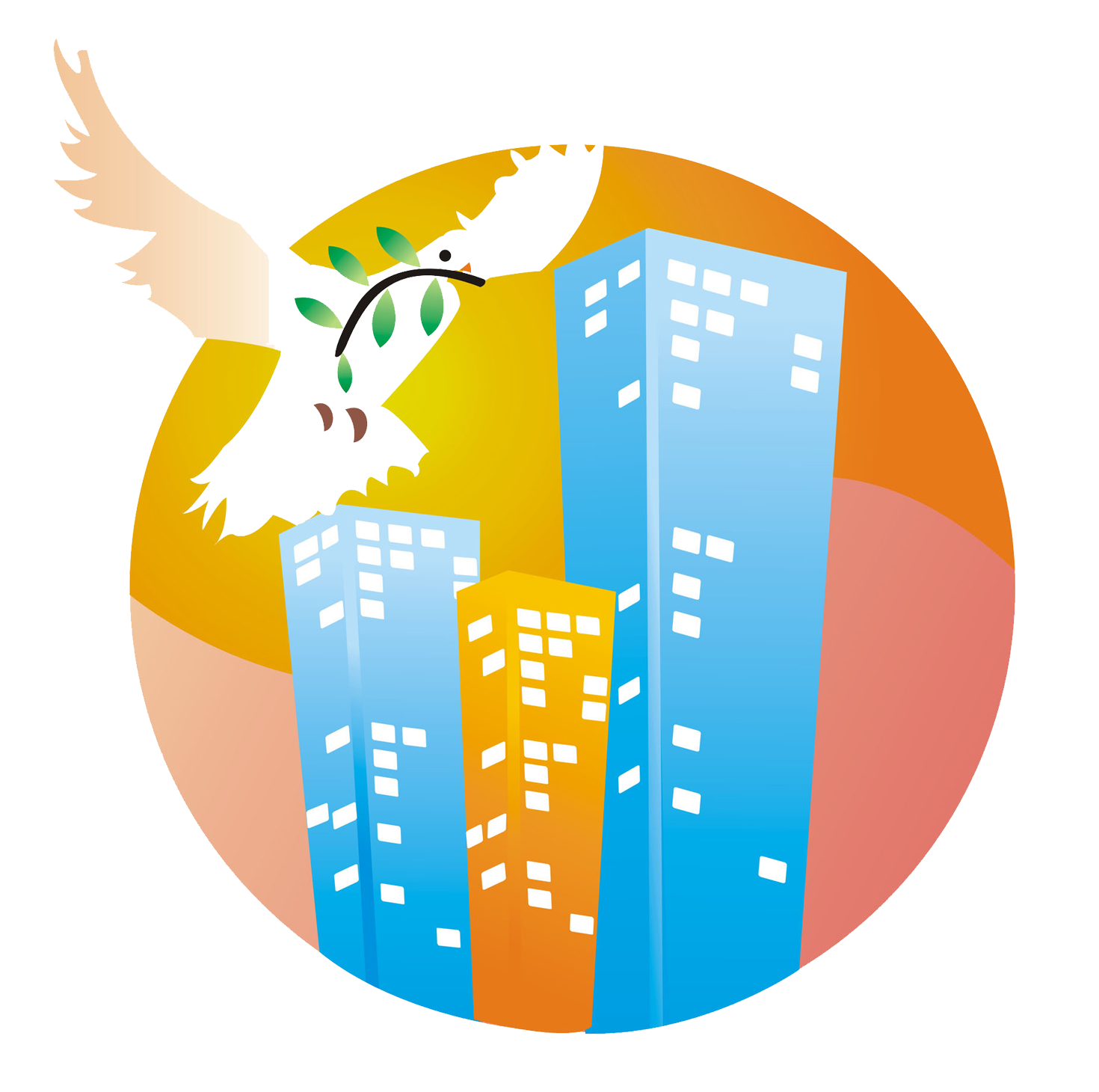
在工业生产中,传统减震缓冲材料如橡胶、EVA、SBR、弹簧等,尽管在某些领域具有一定的应用价值,但其局限性显著,主要体现在以下几个方面:
高频振动过滤能力不足
传统材料(如橡胶、泡沫)主要通过压缩形变吸收低频振动,但在高频振动(>1000Hz)和低幅值冲击(<0.1g)的情况下,其过滤效率较低,甚至容易开裂。例如,在精密数控机床中,传统减震垫会导致加工精度误差显著扩大,从0.01mm增加到0.05mm。耐久性和寿命短
传统材料容易老化和疲劳,使用寿命较短。例如,橡胶材料在高温(>80℃)或低温(<40℃)环境下性能会显著下降,密封失效或硬度增加,导致减震效果大幅降低。此外,某些材料如弹簧在长期使用后会疲劳断裂,需要频繁更换。材料疲劳试验|疲劳试验内容
重量大、体积大
传统减震材料通常体积大、重量重,难以满足航空航天、精密仪器等领域对轻量化和空间利用的严格要求。例如,深海钻井平台使用的聚氨酯隔振器在高压盐雾环境下寿命仅为6个月,维护成本高。适应性差
传统材料难以适应复杂的工作环境。例如,在半导体制造车间,微小的震动偏差可能导致芯片良品率下降30%,直接经济损失巨大。此外,传统材料在极端环境下的性能也受到限制,如橡胶类材料在高温下加速老化,在低温下变硬。环保问题
传统减震吸能材料可能产生有害物质,对环境造成污染。例如,在生产过程中可能释放挥发性有机化合物(VOCs),废弃材料处理不当也会成为环境负担。抗冲击能力有限
传统材料在受到较大冲击力时,往往无法有效分散和吸收能量,导致设备部件损坏。例如,在汽车缓震领域,过重的缓震材料不仅增加油耗,还影响车辆操控性和加速性能。成本高
传统减震材料的制造工艺复杂,成本较高。例如,高端减震缓冲材料如弹簧和橡胶的生产工艺包括碾尖、高温加热、压簧等多个环节,工艺流程繁琐。技术升级困难
传统减震材料的结构复杂、厚重且难以升级,难以满足现代工业对轻量化、智能化的需求。例如,在航空航天和电子芯片领域,传统材料的应用受到限制。
传统减震缓冲材料在高频振动、耐久性、重量、适应性、环保性、抗冲击能力等方面存在显著局限性,难以满足现代工业对高效、环保、轻量化和智能化的需求。这些问题促使新型高性能减震材料(如ACF人工软骨材料)的研发和应用成为趋势